Latest News
Relocation of an entire extrusion line in Australia
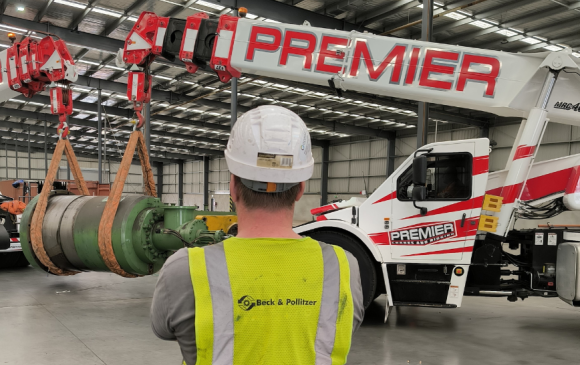
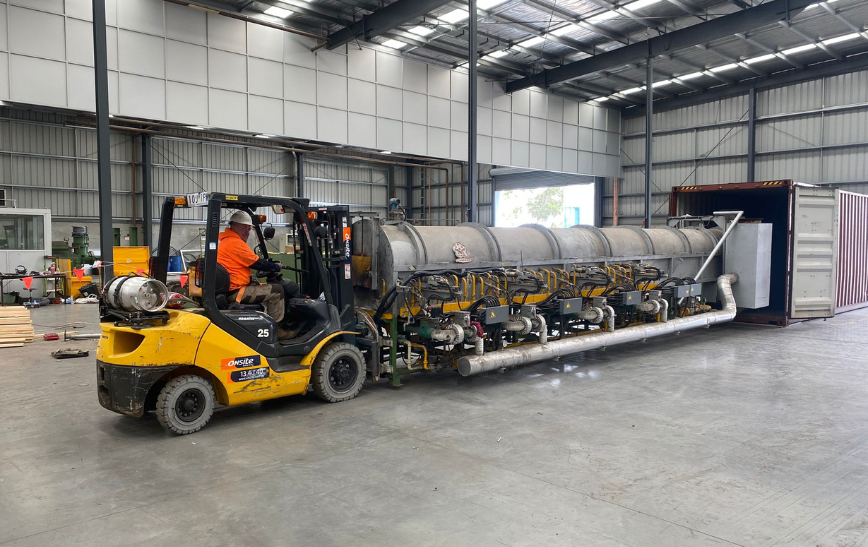
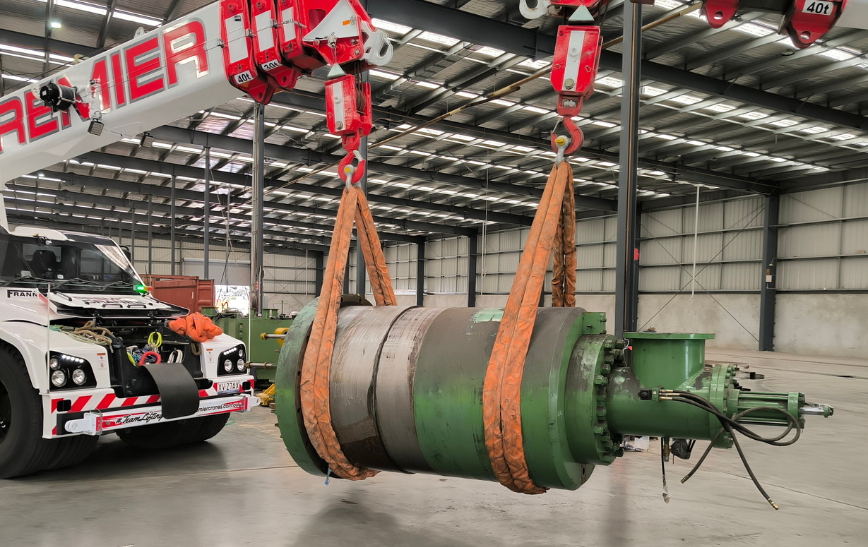
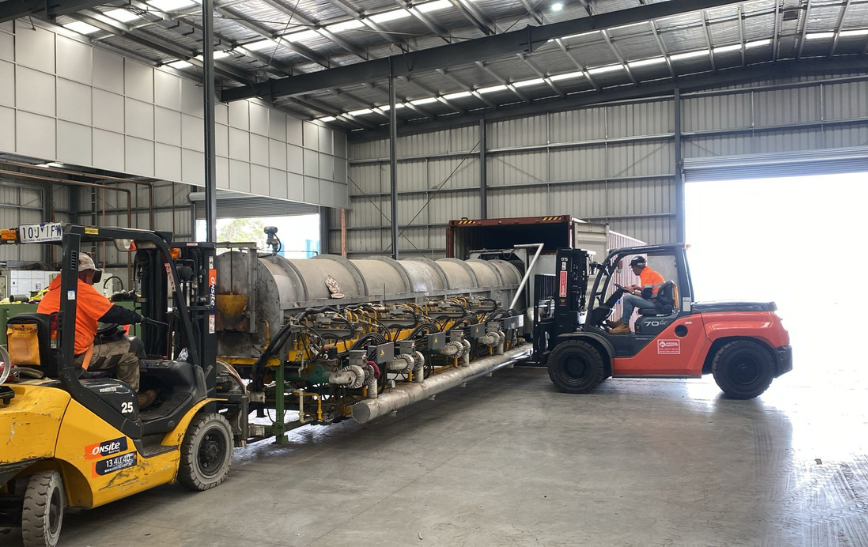
In the annals of industrial feats, few accomplishments rival the relocation of heavy machinery. At Beck & Pollitzer Australia, we recently undertook a monumental task: relocating an entire extrusion line within a compressed timeframe. With precision, expertise, and a dedication to excellence, our team achieved remarkable results. Here’s an insight into our success story:
Unprecedented commitment to safety and efficiency:
Over the course of a rigorous 5-week schedule, Beck & Pollitzer Australia invested a staggering 238,442 project hours into this industrial relocation project. Despite the demanding timeline, our unwavering commitment to safety yielded exemplary results. With zero reported Lost Time Incidents (LTIs) or Medical Treatment Incidents (MTIs), and a spotless record of property damage, our team demonstrated unparalleled professionalism and attention to detail.
Handling heavy loads with finesse:
Central to the project’s success was the meticulous handling of heavy equipment. The extrusion line, totalling 180T in tonnage, along with the main press weighing 130T, posed significant logistical challenges. However, through strategic planning and execution, we managed to transport these massive components with precision and care, utilizing 27 x 40” containers to ensure their safe relocation. Read our article on how to move your heavy machinery safely.
Exceeding expectations in an expedited timeframe:
The project’s timeline was not merely ambitious; it was expedited to meet the urgent requirements of our client. Despite the constraints, Beck & Pollitzer not only met but exceeded expectations. Our program of works, meticulously planned and executed over five weeks, showcased our ability to deliver exceptional results within demanding timeframes.
Environmental responsibility and sustainability:
In line with our commitment to environmental sustainability, we adhered to EPA compliance standards throughout the project. Our specialized processes for oil removal and recycling exemplify our dedication to sustainability. By filtering and repurposing oil, we contribute to environmental conservation and promote responsible industrial practices.
Innovative rigging solutions for cost efficiency:
To optimize efficiency and minimize costs, our team employed innovative rigging solutions, including tandem lifting with 40T Franna cranes, hydraulic jacking, and skates. These advanced techniques not only expedited the relocation process but also proved to be a more cost-effective alternative compared to conventional methods.
Strategic approach for cost savings:
A pivotal aspect of the project involved devising cost-effective solutions tailored to our client’s needs. While alternative methods may have included lifting the main press without stripping, logistical constraints and transportation costs necessitated a different approach. Our specialised team meticulously stripped all components, match-marked them, and loaded them into containers. All electrical components and wiring have been disconnected and labelled, disconnect and reconnect documents supplied to the client to provide a seamless installation and commissioning at the relocation destination. This strategic approach resulted in significant cost savings for our client without compromising quality or safety.
Accompanying this narrative are select photos that capture the essence and magnitude of our achievement – these images serve as a visual testament to our commitment to excellence and innovation.
In conclusion, Beck & Pollitzer Australia’s successful relocation of the extrusion line stands as a testament to our expertise, dedication, and unwavering commitment to excellence. As we continue to push the boundaries of what is possible in industrial engineering, we remain steadfast in our pursuit of innovation and customer satisfaction. To discuss your machinery relocation needs please contact us for further advice and assistance.
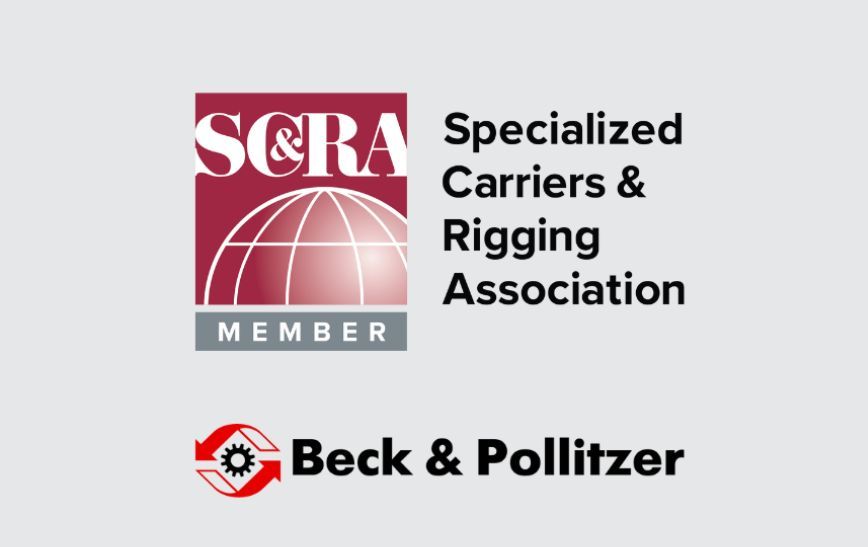
Beck & Pollitzer joins prestigious SC&RA network
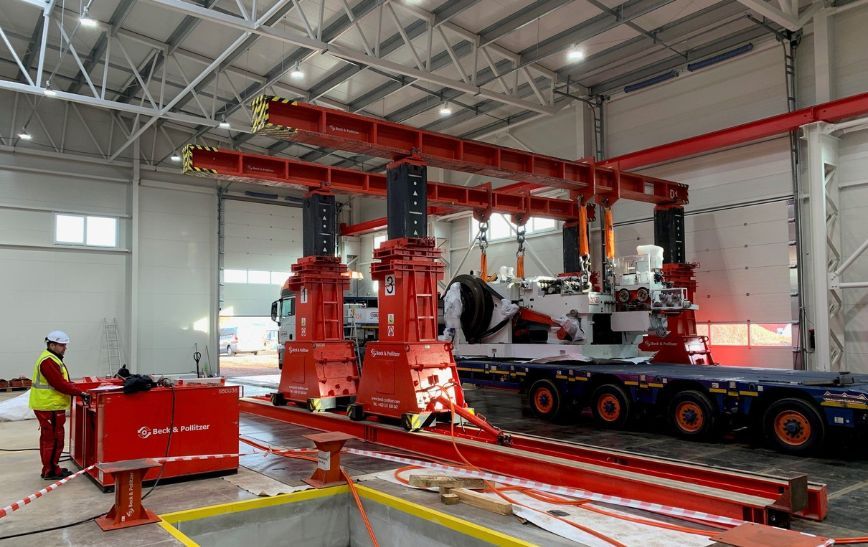
Industrial press installation successfully delivered in Žacléř, Czech
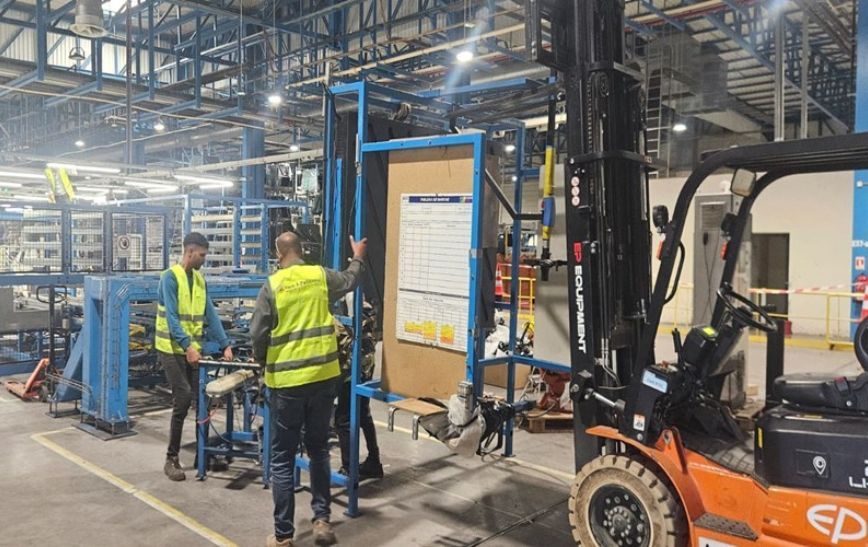
Glass Manufacturing: Cross-border production cell relocation
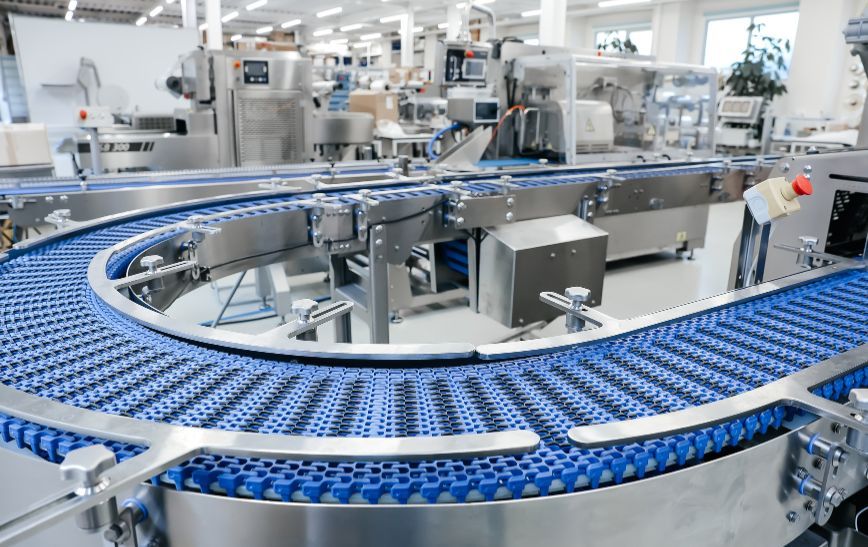
Beck & Pollitzer Polska: Italian production line relocation mastered
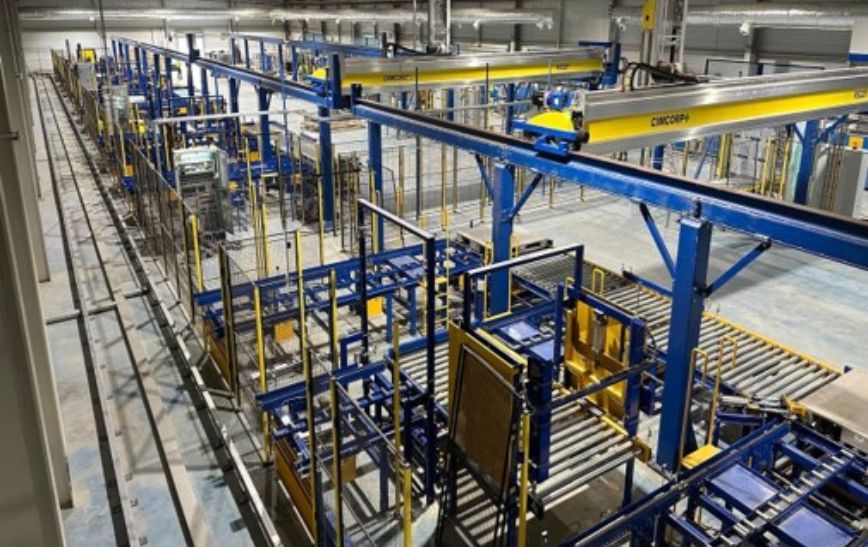