News
Comprehensive conveyor systems guide: Boosting efficiency and safety
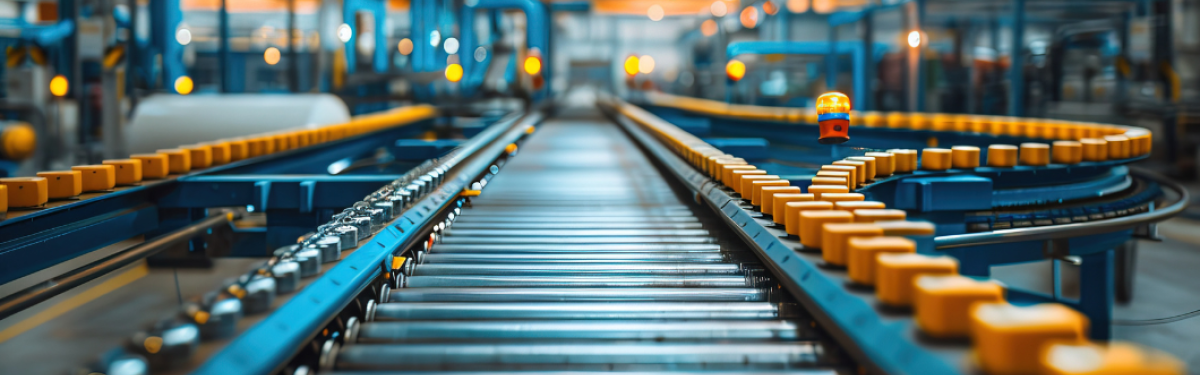
Maximizing production line efficiency with conveyor systems: A complete overview
Conveyor systems are essential to modern manufacturing and logistics, providing efficient material handling solutions that streamline production lines and distribution centers. The global conveyor systems market is expected to reach USD 7.76 billion by 2029, growing at a CAGR of 4.8%. This growth is driven by the increasing demand for automation and efficiency in various industries.
Whether you are a business considering installing a conveyor system for the first time or an existing manufacturer looking to improve your production line efficiency, this guide covers all you need to know about conveyors.
What are conveyor systems?
Conveyor systems are automated mechanical devices designed to transport materials or products from one location to another within a facility. These systems consist of a series of frames, belts, rollers, chains, or wheels that work together to move items efficiently and safely across different stages of production or distribution. By automating the movement of materials, conveyor systems significantly enhance operational efficiency and productivity. These systems are used across various industries, including manufacturing, warehousing, distribution, and more.
Industries utilizing conveyor systems:
- Manufacturing: Conveyor systems efficiently move raw materials, parts, and finished products throughout production, streamlining continuous or batch processes. They enhance workflow, reduce manual handling, and increase overall productivity, ensuring timely delivery of products.
- Food and beverage: Transport ingredients and packaged goods while maintaining hygiene standards. They ensure compliance with health regulations, reduce contamination risks, and support high-speed processing and packaging operations to meet consumer demand.
- Mining and heavy industries: Uses conveyor systems to move large quantities of bulk materials, such as coal, ores, and minerals. Conveyors are critical for material extraction, processing plants and transporting materials to stockpiles.
- Warehousing and distribution: Facilitate the efficient movement of goods within large storage areas, helping with sorting, packing, and shipping. These systems optimize space utilization, improve inventory management, and speed up order fulfilment processes.
Benefits of conveyor systems:
Conveyor systems offer a multitude of advantages over manual material handling:
- Increased efficiency: Conveyor systems automate the transportation of materials, significantly enhancing the speed and efficiency of operations. By moving goods consistently and quickly, these systems help businesses meet production targets and deadlines more effectively.
- Improved safety: By automating the transportation of heavy or hazardous materials, conveyor systems reduce the risk of workplace injuries, contributing to a safer work environment. They also minimize human interaction with dangerous machinery and materials, further enhancing overall workplace safety standards.
- Cost savings: Automation with conveyor systems reduces labor costs and minimizes errors, leading to significant cost savings over time. In addition, Modern conveyor systems are designed for durability and require minimal maintenance, reducing long-term maintenance expenses.
- Flexibility: Conveyor systems can be customized to fit specific operational needs, accommodating various load types, sizes, and shapes. hey can be easily reconfigured or expanded to adapt to changing production demands, ensuring long-term usability.
- Enhanced ergonomics: Conveyor systems help maintain proper posture and reduce strain on workers, promoting a healthier work environment. By automating repetitive tasks, they also decrease the risk of musculoskeletal disorders and increase worker productivity.
- Inventory management: Conveyors efficiently move materials through production stages, improving inventory control and reducing bottlenecks. This streamlined flow enhances tracking accuracy and minimizes delays, ensuring a more responsive supply chain.
- Space optimization: Conveyor systems can be configured to utilize vertical space, maximizing floor area for other operations. This efficient use of space supports higher throughput and can accommodate future growth without requiring extensive facility modifications.
- Enhanced ergonomics: Conveyor systems help maintain proper posture and reduce strain on workers, promoting a healthier work environment. By automating repetitive tasks, they also decrease the risk of musculoskeletal disorders and increase worker productivity.
- Inventory management: Conveyors efficiently move materials through production stages, improving inventory control and reducing bottlenecks. This streamlined flow enhances tracking accuracy and minimizes delays, ensuring a more responsive supply chain.
- Space optimization: Conveyor systems can be configured to utilize vertical space, maximizing floor area for other operations. This efficient use of space supports higher throughput and can accommodate future growth without requiring extensive facility modifications.
Types of conveyor systems:
The diverse world of conveyors offers solutions for a wide range of material handling needs. Here are some of the most common types:
-
Belt conveyors
These are the most common type, using a continuous belt to transport materials. They are ideal for moving products of various shapes and sizes over long distances. Belt conveyors are often used in industries such as food processing, manufacturing, and mining. They can be made from a variety of materials including rubber, PVC, and fabric, allowing for customization based on the specific requirements of the application. Additionally, they can be designed with different inclines and curves to navigate complex layouts.
-
Roller conveyors
Roller conveyors consist of a series of rollers that allow items to be moved manually or by gravity. They are suitable for transporting heavier items and can be used in packaging and assembly lines. Roller conveyors can be powered or non-powered (gravity conveyors). They are highly flexible, allowing for easy integration into existing systems. They are commonly used in industries such as automotive, warehousing, and logistics. Their modular nature makes them easy to expand and reconfigure as needed.
-
Chain conveyors
These use chains to move products along the production line and are ideal for heavy-duty applications like automotive manufacturing. Chain conveyors are known for their durability and ability to handle very heavy loads, making them perfect for transporting pallets, containers, and large industrial parts. They are often used in harsh environments where other conveyor types might fail. Their design can be customized with different chain types and layouts to meet specific operational needs.
-
Pneumatic conveyors
Pneumatic conveyors use air pressure to transport materials through tubes. They are suitable for moving bulk materials such as powders and granules. These systems are ideal for applications that require a clean and dust-free environment, such as pharmaceuticals, food processing, and chemical manufacturing. Pneumatic conveyors can be configured for both dense and dilute phase conveying, allowing for versatility in handling different types of materials. They also offer flexibility in routing materials through complex layouts.
-
Overhead conveyors
These systems use overhead tracks to move items, freeing up floor space and allowing for more efficient use of the available area. Overhead conveyors are often used in manufacturing plants, automotive assembly lines, and paint shops. They can handle a variety of loads, from light items to heavy parts. These systems are particularly useful in environments where space is at a premium or where items need to be transported over long distances without interfering with floor-level operations. They can also be designed to move products through different levels and around obstacles.
Important aspects of conveyor systems
- Design and customization: Selecting the right conveyor system involves understanding your operational needs and customizing the system to fit those requirements. This includes choosing the right type of conveyor, determining the appropriate load capacity, and ensuring compatibility with existing equipment.
- Installation and assembly: Proper conveyor installation and assembly are crucial for optimal performance. This includes precise alignment, secure fittings, and thorough testing to ensure the system operates smoothly and safely.
- Safety features: Safety should be paramount. Ensure your chosen conveyor system complies with safety regulations and includes safeguards like emergency stops.
- Maintenance and support: Regular maintenance is essential to keep conveyor systems running efficiently. This includes routine inspections, timely repairs, and replacement of worn-out components. Partnering with experienced service providers can help ensure your system remains in top condition.
- Scalability: As your business grows, your conveyor system should be able to scale accordingly. Modular designs and expandable components can help accommodate increased production volumes and changing operational needs.
Conclusion:
Investing in a conveyor system can significantly enhance your operational efficiency, improve safety, and reduce costs. By understanding the different types of conveyor systems and their benefits, you can make informed decisions that align with your business needs.
For businesses considering their first installation or looking to upgrade their existing systems, partnering with experienced professionals like Beck & Pollitzer is crucial to ensure long-term success. With over 160 years of experience in industrial and engineering services, Beck & Pollitzer offers a comprehensive range of conveyor solutions tailored to your specific requirements.
Our team of experts can guide you through every stage of the process, from initial consultation to installation, commissioning, and ongoing maintenance. We leverage our vast knowledge and proven track record to ensure your conveyor system is installed and maintained to the highest standards, maximizing your return on investment.
Contact our highly experienced team of conveyor installers to discuss your conveyor installation project!