Latest News
10 Tips for a seamless production line relocation process
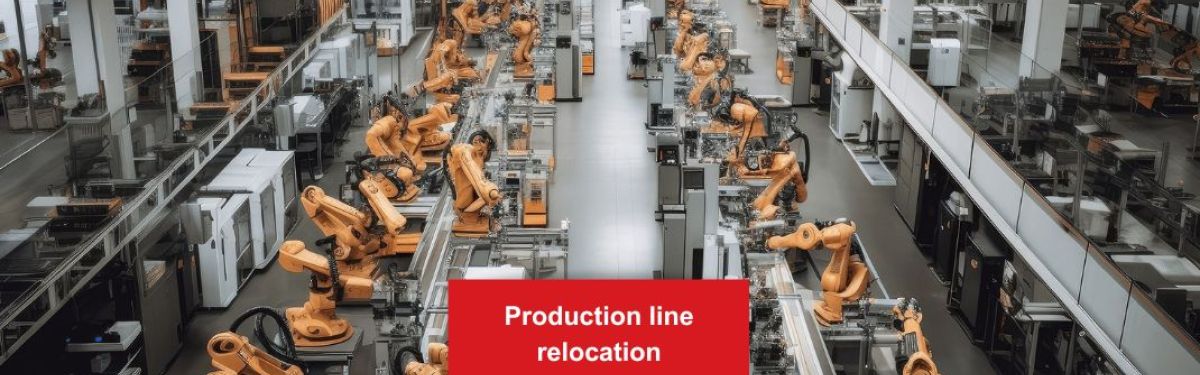
Production and manufacturing lines are systems designed to efficiently produce goods or process materials on a large scale. In today’s dynamic business landscape, operational agility and strategic decision-making are paramount. As industries evolve and markets shift, companies often find themselves facing the challenging task of relocating their production and manufacturing lines.
The process of relocating a production line can be complex and requires careful planning and execution. Here is a general outline of the steps involved:
-
-
- Needs Assessment:
Identify the reasons for the production line relocation, such as cost reduction, expansion, or strategic considerations. Assess the new location’s suitability based on factors like labour availability, infrastructure, proximity to suppliers and customers, regulations, and market access. - Planning:
Develop a detailed relocation plan that outlines the timeline, resources, and budget required for the move. Define the relocation process’s objectives, milestones, and key performance indicators (KPIs). - Facility design and preparation:
Design the new production facility layout, considering factors such as workflow optimisation, equipment placement, safety requirements, and future scalability. Prepare the new facility by ensuring necessary utilities, infrastructure, and permits are in place. - Equipment evaluation and selection:
Evaluate the existing production equipment to determine if it can be relocated or if new equipment needs to be procured. Assess the compatibility of the equipment with the new facility and production requirements. Plan for any necessary modifications, upgrades, or replacements. - Supply chain management:
Review the supply chain and logistics involved in moving the production line. Coordinate with suppliers to ensure a smooth transition, including shipping timelines, inventory management, and potential disruptions in the supply of raw materials or components. - Employee transition and training:
Communicate the relocation plans to employees and provide support throughout the transition. Determine the workforce requirements in the new location and assess the need for hiring, retraining, or transferring employees. Develop a training plan to familiarise the workforce with the new equipment, processes, and safety protocols. - Transition execution:
Implement the relocation plan by coordinating the physical movement of equipment, inventory, and materials to the new location. The process involved three main phases:-
- Disassembly of the production lines:
The disassembly of production lines plays a crucial role in ensuring the smooth transition of lines from one location to another. Firstly, form a skilled team that will carefully dismantle the machinery and components, ensuring that each item is marked and documented for reassembly. This documentation will serve as a valuable reference during the reassembly phase. Next, utilise appropriate lifting and loading equipment, such as hydraulic gantries, versa lifts, and forklift trucks, to safely lift and load the dismantled machinery onto transportation vehicles. - Production line transport:
The transport phase is a critical stage in the relocation of production and manufacturing lines and having the right tools for machine transportation is essential to ensure a safe and successful move. In today’s technologically advanced landscape, machinery has become heavier and more sophisticated, demanding utmost accuracy during transportation.To achieve this, utilising metrology techniques such as laser tracking can be invaluable. Metrology systems, including floor-marking, alignment, measuring, and levelling, contribute to pinpoint precision throughout the entire transport process. By incorporating these practices, companies can ensure the secure and accurate relocation of their machinery, minimising the risk of damage and maximising efficiency. - Reassembly of the production lines:
During the assembly and launch phase at the new site, it is crucial to focus on a successful machinery installation that aligns with your requirements, timelines, and budget. A key aspect is to establish a collaborative partnership with the installation team to ensure effective communication and coordination. Whether it involves installing a single manufacturing line or relocating entire factories, prioritise commissioning support and testing to guarantee optimal functionality.
- Disassembly of the production lines:
-
- Quality control and assurance:
Establish quality control procedures in the new facility, ensuring that products meet the required standards. Conduct thorough check-ups, dry runs, and verifications to validate the machinery’s performance and alignment with production targets and to address any issues during the transition period. - Customer and stakeholder communication:
Communicate the relocation to customers, suppliers, and other stakeholders, providing them with updated contact information and addressing any concerns or potential disruptions in the supply chain. Maintain open lines of communication to ensure a smooth transition and minimise the impact on business relationships. - Monitoring and optimisation:
Monitor the performance of the relocated production line, track key metrics, and compare them against predefined KPIs. Identify areas for improvement and optimize processes to enhance productivity, quality, and efficiency.
- Needs Assessment:
-
How Beck & Pollitzer can help with your relocation projects
It’s important to note that the specific steps and considerations may vary depending on the nature of the production and assembly line, industry, and the unique requirements of the relocation. Engaging with professionals such as Beck & Pollitzer, who have experience in production/assembly line relocation and project management, can greatly facilitate the process.
Our expert team, consisting of project managers, supervisors, millwrights, riggers, fitters, electricians, pipefitters, and welders, is equipped with the latest lifting and machinery removal equipment to handle even the most complex relocations and installations projects. With 160 years of engineering experience and knowledge across various industries, we have demonstrated exceptional success in delivering projects of all sizes. Safety is our top priority, and we adhere to global health and safety standards to ensure a zero-accident culture.
With our commitment to listening, partnership, on-time delivery, and staying within budget, we are dedicated to providing a successful production and manufacturing line relocation experience for our clients worldwide. Call your local branch for your next project!