Latest News
What it takes to create a Gigafactory
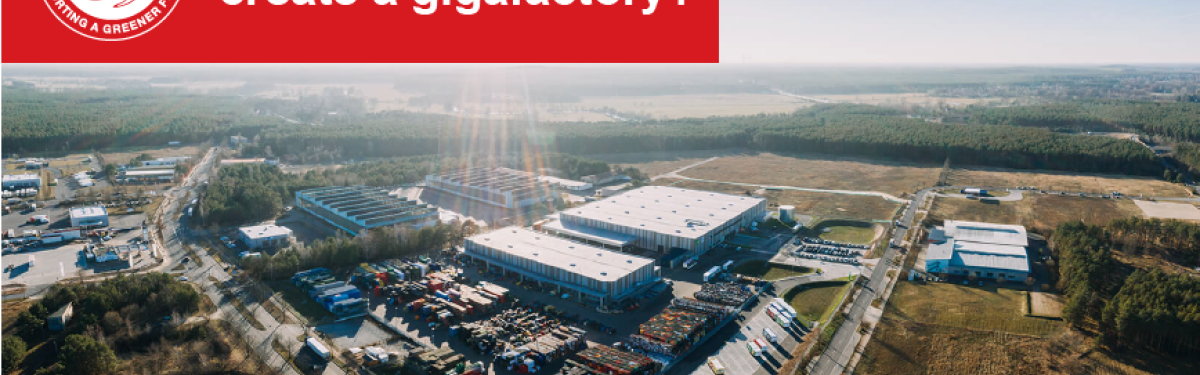
Gigafactories — the long, hard road from announcement to delivery.
‘We are proud and delighted to announce….’
Barely a week goes by without someone declaring to the world’s press that they’re establishing a new Gigafactory in China, Europe, or the USA. It’s proof, in case anyone needed it, that Battery Electric Vehicles (BEV) are the future. Plenty of excitement always surrounds the prospect of launching a new plant focusing on cell production or battery assembly. But after the initial fanfare, cold, hard reality sets in. There’s so much work to do.
Here we look at the toil and trouble the project team has to endure on the treacherous road from announcement to delivery of a Giga factory.
Financing the Gigafactory project
No project gets to the big announcement stage without having a set of investors in place who have commitments from various partners to get the giga factory off the ground. But verbal agreements are one thing. Achieving the various financing milestones is a far more significant challenge.
First, there’s the need to seal a deal to ensure demand from a specific company for whatever the Gigafactory plans to make — pouches, prisms, solid-state, etc. Then the financiers need to find the land on which to build their plant (more on that shortly). And, as much of this is a new technology, there’s often a need to invest in a pilot plant which needs to prove that the product the Gigafactory is proposing to make can be made profitably —all before breaking ground on the main facility.
These key milestones often take years of planning, with big teams of experienced financial experts and engineers thrashing out the finer details.
Finding the location for your Gigafactory
Assuming the financing is agreed upon, the next task is to decide where this is all going to happen. Creating battery cells is energy-intensive. A regular, reliable and dedicated supply of electricity and water is crucial. Any breaks in the flow will affect the production schedule and could cost $millions.
The amount of electricity required to run a Gigafactory is eyewatering. For example, the Northvolt Ett plant in Sweden, a venture involving the Volkswagen Group, already received $1 billion in investment. It is estimated to require 2TWh, the equivalent of 2% of Sweden’s annual electricity consumption. Another study revealed that battery cell factories use around 50-65 kWh of electricity per kWh battery capacity.
It is clear how much importance location plays in ensuring easy and constant access to resources. But there are other considerations to take into account when deciding on a location for a Gigafactory.
A key one is the stability of the political landscape in the chosen region. Unrest and uncertainty are the business enemies, so selecting a country with a settled political picture and strong leadership often pays dividends. And a connected point needing consideration is how sympathetic the local government is to the production of cells and batteries. Both are designed to help countries meet sustainability and carbon reduction goals, exactly the kind of industry many nations want to attract. So much so, some governments are offering incentives for businesses to set up such factories. For example, Reuters revealed in September 2020 that India was planning to make $4.6 billion in incentives available to battery makers.
Also, the ease with which raw materials can be accessed and transported to the plant is a major factor. So too is the location of the final customer for the finished product, taking into account the logistical (transportation) and tax implications.
And who are the people who are going to run the Gigafactory coming from? Is there a pool of suitably qualified local talent that the Gigafactory operators can pick from, or will they need to cast their recruitment net further and wider — a potentially more expensive option?
Any Gigafactory owner has plenty to think about before taking the plunge and planting their flag in the ground of one location ahead of another. Often, long-held principles go out of the window, evidenced by Ineos, a company that proclaimed itself the champions of the ‘Made In Britain’ ethos and yet chose in the end to manufacture its product in Hambach, France, rather than Bridgend, Wales. The financial case was just too good to ignore!
Whichever location is decided upon, the clock starts ticking then. With finance in place and buyers awaiting the product, now the action phase begins. Engineers take over, and all decisions made from hereon have a direct impact on the future profitability of the Gigafactory.
Proving the Gigafactory concept
The next phase isn’t actually jumping straight into building the full-size production plant. It is vital to fine-tune the design process, the chemistry and proves that the concept works. And most organisations choose to do this by developing a pilot plant. This is a smaller scale model of the planned full-size production plant, the blueprint on which future ways of working on a larger scale will be based. And the creation of the pilot plant takes the skills of designers, procurement specialists and engineers. Only by proving that what they planned to make can be made at a profit can this hurdle be overcome, and the financing for the project released, ready for the Industrialisation phase.
Securing the Gigafactory machinery
The rush to meet the demand for cell and battery production has left OEMs struggling to keep up with requests. Machinery is in high demand, and those manufacturing it are few and far between. Most are in Asia, specifically Korea, Japan, and China. Manufacturers in Germany are beginning to up their game, but they’re still years behind their more established counterparts in the Far East.
It is virtually impossible to build a 100% European giga factory due to the lack of suppliers. And lead times in Europe to deliver machines that build the cells are measured in years rather than months. A 2019 McKinsey report revealed that projected battery demand from BEVs produced in Europe was five times higher than the production capacity of European-based manufacturers. This limited availability of OEMs is forcing some Gigafactory owners to compromise their principles and secure machinery from second-rate manufacturers. It’s a case of needs must.
Delivering the Gigafactory
Assuming the previous obstacles have been overcome, now comes the time to build the Gigafactory, install the machinery, check its safety, and recruit and train the people who will make it all happen — another critical phase of the process that is often prone to delays. Construction can be knocked off schedule by bad weather, problems with supply chains, and external factors. These include problems securing the correct environmental permits, such as Tesla’s Berlin Gigafactory production project is facing. And, of course, global pandemics can wreak havoc with schedules.
With all these factors occupying the minds of Gigafactory owners, the actual installation and commissioning of the machinery that will make the Gigafactory work can slide down the scale of importance. But it is critical because the timely installation of the heavy machinery will directly impact the date when the Gigafactory finally starts to make money.
With so many hurdles to overcome and complexities to solve, it’s a small wonder that many of the first wave of BEV start-ups from around 5 years ago are no longer with us – think Faraday Future, Fisker, Nikola’s delays. There’s a need for the sector to mature fast and use the expertise available to meet the colossal demand so that the process of delivering the Gigafactories the world needs becomes far easier.
Beck & Pollitzer is currently playing a major role in installing Gigafactory machinery and supporting bluechip cell manufacturers worldwide.
Interested in learning more about Gigafactories? Our article explores their size, power, and sustainability – give it a read!