Latest News
What is Industry 4.0? An overview of the Fourth Industrial Revolution
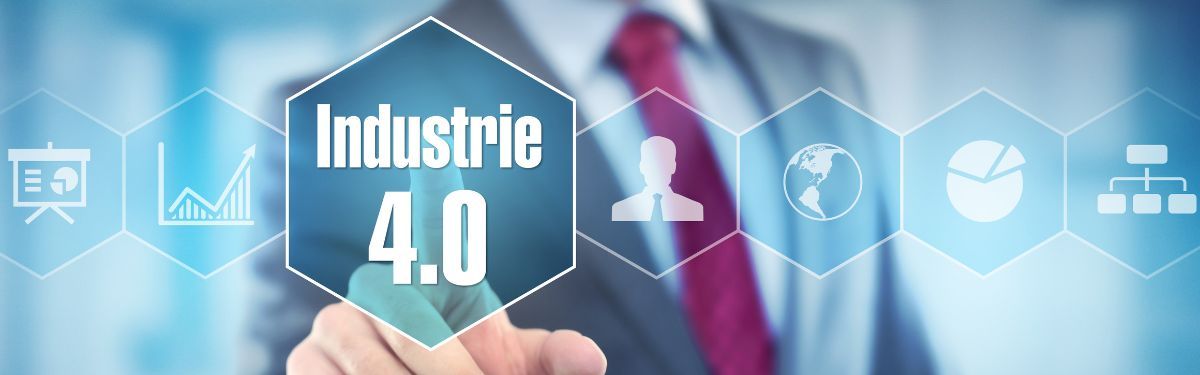
Industry 4.0, also known as the Fourth Industrial Revolution, represents a transformative shift in how industries operate. It integrates advanced technologies such as the Internet of Things (IoT), artificial intelligence (AI), and robotics to create smarter, more efficient, and interconnected systems. This article explores the origins, core technologies, and implications of Industry 4.0, highlighting its role in revolutionising manufacturing and other sectors.
The origin of Industry 4.0
The term “Industry 4.0” was first introduced in 2011 at the Hannover Fair, a major trade show in Germany. It marked the beginning of a strategic initiative to drive digital transformation across industries. The name refers to the fourth wave of industrial evolution:
- First Industrial Revolution: Mechanisation powered by water and steam engines.
- Second Industrial Revolution: Mass production driven by electricity and assembly lines.
- Third Industrial Revolution: Automation enabled by computers and electronics.
- Fourth Industrial Revolution: Smart and autonomous systems driven by data, AI, and connectivity.
So, when did Industry 4.0 start? While its roots date back to 2011, its widespread adoption has accelerated over the past decade with advancements in Industry 4.0 technologies.
What is Industry 4.0?
Industry 4.0 refers to the integration of digital and physical systems in industries, creating a seamless network of connected devices and intelligent systems. These technologies leverage real-time data to optimise operations, enhance decision-making, and deliver unprecedented efficiency.
Key Industry 4.0 technologies – Several cutting-edge technologies form the backbone of Industry 4.0:
Internet of Things (IoT)
The IoT connects devices, sensors, and machinery across manufacturing processes to facilitate seamless communication and data exchange. By integrating IoT, businesses can enable real-time monitoring, predictive maintenance, and automated adjustments. For example, sensors on a production line can detect anomalies and notify operators before a breakdown occurs, minimising downtime and boosting efficiency.
Artificial Intelligence (AI)
AI is the brain behind Industry 4.0, enabling machines to learn, adapt, and make intelligent decisions. AI algorithms can analyse vast amounts of data collected from sensors and machines to predict equipment failures, detect quality defects, and optimise production schedules. For example, AI-powered vision systems can inspect products for flaws with greater accuracy and speed than human inspectors, ensuring consistent quality control.
System Integration/Robotics
Modern robotics plays a vital role in automating repetitive, high-precision tasks. Robots in Industry 4.0 are no longer limited to static operations. Collaborative robots, or “cobots,” work alongside humans, adapting to dynamic environments. This system integration enhances production speed, reduces errors, and frees up human workers for more complex tasks.
Cloud Computing
Cloud computing provides the backbone for data storage and processing in Industry 4.0 It allows businesses to access and analyse data remotely, share insights across global teams in real-time, and scale resources up or down based on operational needs. By moving to the cloud, companies reduce infrastructure costs and improve collaboration across departments and locations.
Big Data Analytics
The massive amounts of data generated by IoT devices and other systems are processed using big data analytics. This technology helps companies identify inefficiencies in production, monitor supply chain performance, and improve decision-making through actionable insights. For example, manufacturers can use analytics to optimise energy usage, reduce waste, and improve output quality.
Additive Manufacturing (3D Printing)
Additive manufacturing allows companies to create complex, custom parts quickly and cost-effectively. This technology supports rapid prototyping, enabling engineers to test and refine designs in less time, and mass customisation, allowing businesses to produce small batches tailored to specific customer needs.
Augmented Reality (AR) and Virtual Reality (VR)
AR and VR technologies are transforming how businesses train employees, maintain equipment, and execute complex tasks. AR and VR simulations provide immersive training environments, improving skills without risking real equipment.
Cybersecurity
With interconnected systems comes the increased risk of cyber threats. Cybersecurity ensures the protection of sensitive data, intellectual property, and operational systems. As companies adopt Industry 4.0 technologies, cybersecurity becomes a top priority to ensure operational resilience and trust.
Why is Industry 4.0 transforming manufacturing?
Industry 4.0 manufacturing is at the forefront of this revolution, offering numerous benefits:
- Enhanced efficiency: Automated processes reduce production time and resource waste.
- Improved quality: Advanced sensors and AI ensure consistent and high-quality output.
- Customisation: Flexible production systems enable mass customisation.
- Cost savings: Predictive maintenance and optimised supply chains reduce expenses.
- Sustainability: Efficient resource management minimises environmental impact.
Beyond manufacturing: Industry 4.0 across industries
The influence of Industry 4.0 extends beyond manufacturing are not limited to manufacturing. Other industries such as retail, healthcare, logistics, and energy sectors are also adopting Industry 4.0 solutions to boost productivity and innovation.
- Healthcare: Improving patient care through AI-powered diagnostics, remote monitoring, and personalised medicine.
- Energy: Optimising energy consumption, enabling smart grids, and promoting renewable energy sources.
- Transportation: Developing autonomous vehicles, optimising traffic flow, and enhancing logistics.
- Agriculture: Implementing precision agriculture techniques to increase yield and sustainability.
Industry 4.0 solutions: A glimpse into the future
Companies are embracing Industry 4.0 technology to remain competitive in a rapidly evolving market. Smart factories equipped with IoT sensors and AI systems are enabling real-time decision-making. Automated warehouses, drone deliveries, and AI-driven supply chains are becoming the new norm.
Embracing the future of Industry 4.0 with Beck & Pollitzer
Adopting Industry 4.0 technologies can be a complex process, but with the right partner, it becomes seamless. At Beck & Pollitzer, we specialise in providing tailored solutions to help businesses embrace the Fourth Industrial Revolution. Our extensive services include machinery installation, relocation, and industrial maintenance, all designed to support digital transformation across industries.
We have expertise in diverse sectors, including warehouse automation, where we enable smart logistics systems, and the rapidly evolving battery and electrification industry, supporting the transition to electric vehicles. With decades of experience and a global presence, Beck & Pollitzer ensures that your Industry 4.0 implementation is efficient, reliable, and aligned with your business goals.
Contact us today to learn more about our services and how we can help your organisation thrive in the era of Industry 4.0.