Latest News
Streamlined fridge production line disassembly and relocation
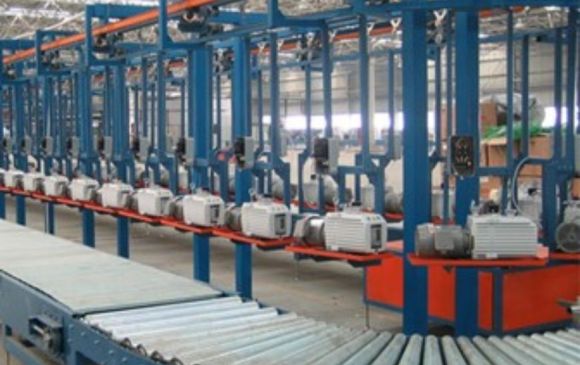
Blue-Chip Client Chooses Beck & Pollitzer for Flawless Disassembly & Relocation
Beck & Pollitzer recently tackled a complex project for a renowned European blue-chip client, showcasing our expertise in minimising production downtime while seamlessly disassembling and relocating critical infrastructure.
The challenge – Dismantling and relocating two entire fridge production lines, with one set requiring meticulous disassembly for reassembly at a new site.
Phase 1: Surgical precision in a live environment
Our team began by scrapping the second production line responsibly, maximising material recovery through efficient recycling processes. Simultaneously, we embarked on the delicate task of disassembling four key machines: a packaging machine, vacuum forming machine, door foaming machine, and pre-assembly line. Every step was meticulously documented, with electrical disconnection sheets, detailed diagrams, and even GoPro footage captured to ensure seamless reassembly at the new location.
Disassembled machinery:
- 1x Packaging machine
- 1x Vacuum forming machine
- 1x Door foaming machine
- 1x Pre-assembly line
- 1x Assembly line
- 1x Packing line
- 1x Foaming machine
- 1x Sheet metal forming machine
- 1x Laser cutting machine
- 1x Puffer lift
Phase 2: International collaboration ensures smooth transitions
Collaboration played a vital role in this project’s success. We worked closely with the receiving country to develop a standardised marking and documentation system, guaranteeing the foaming machine’s accurate reconstruction abroad.
Phase 3: Minimising disruption while maximising efficiency
With the first production line located adjacent to active production areas, meticulous planning and strict safety protocols were paramount. Our team employed strategic logistics to minimise any disruption to the client’s ongoing operations. The successful deployment of 42 vehicles further demonstrates our ability to handle large-scale equipment movements with precision and efficiency.
Results:
Beck & Pollitzer successfully completed the disassembly and relocation of two fridge production lines within a 3-month timeframe, exceeding the client’s expectations. We delivered a sustainable machinery moving solution through responsible recycling, preserved operational continuity through meticulous planning, and fostered successful international collaboration.
Looking for a trusted partner to handle your complex industrial relocation needs? Contact Beck & Pollitzer today and experience the difference!
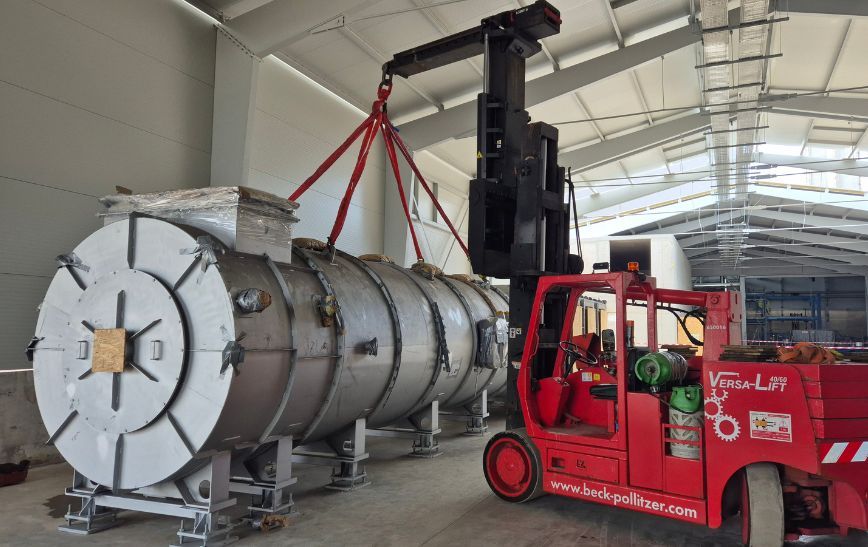
Industrial oven installation: Showcasing advanced rigging expertise
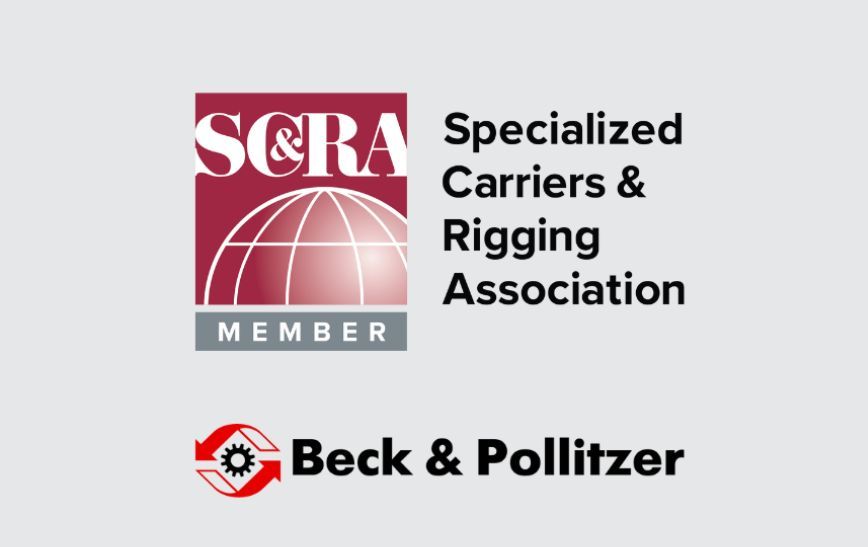
Beck & Pollitzer joins prestigious SC&RA network
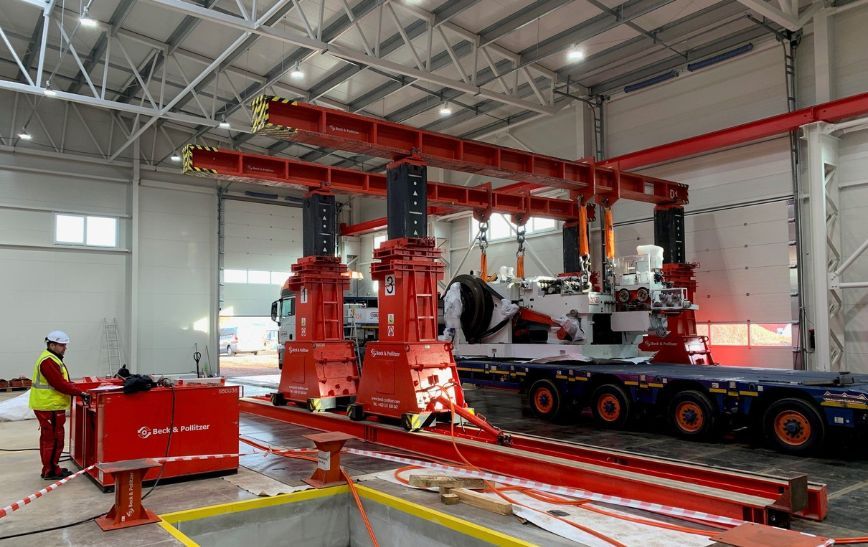
Industrial press installation successfully delivered in Žacléř, Czech
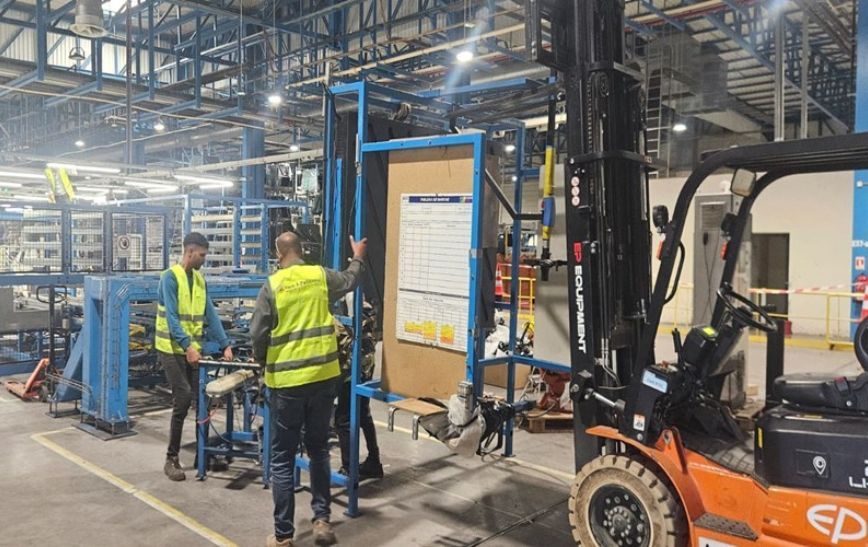
Glass Manufacturing: Cross-border production cell relocation
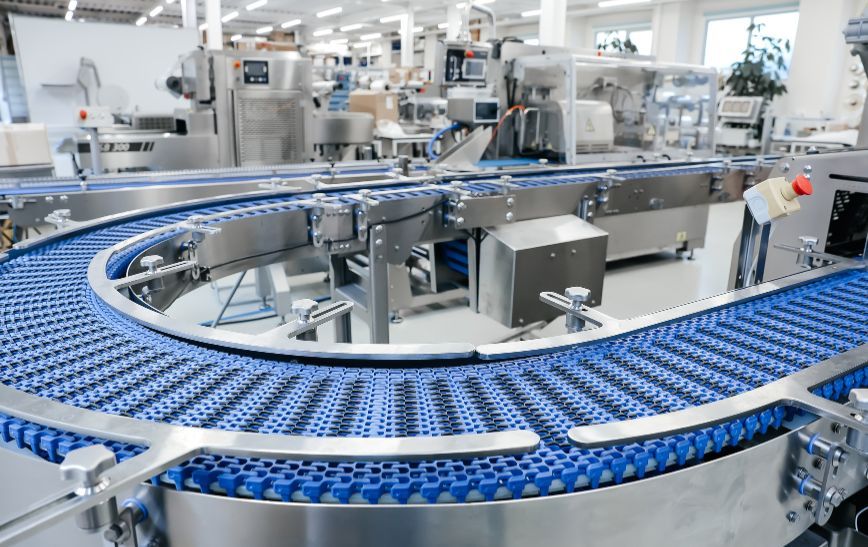