Latest News
Implementing Industry 4.0 in assembly processes: A practical guide
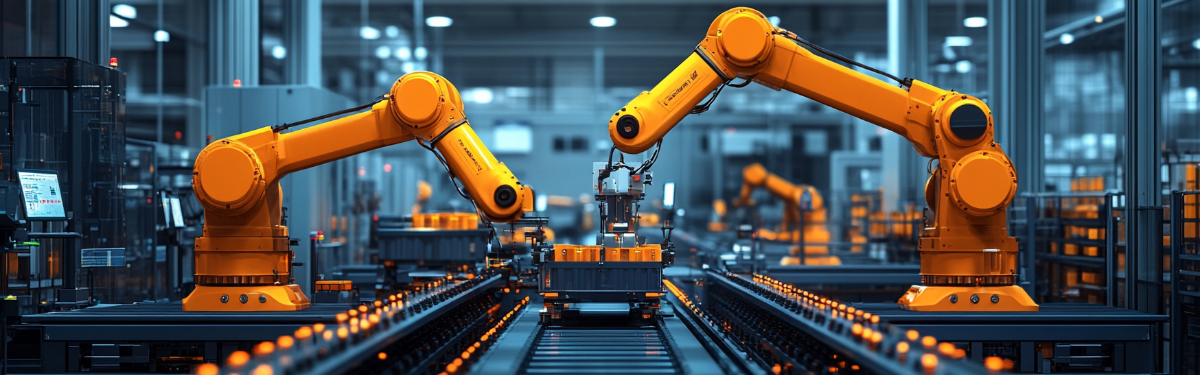
Industry 4.0, the fourth industrial revolution, is reshaping the manufacturing landscape. By integrating digital technologies, manufacturers can streamline assembly processes, improve product quality, and boost overall efficiency. This article provides a practical guide to implementing Industry 4.0 in assembly processes.
Why Industry 4.0 is essential for the assembly process
The assembly process often involves repetitive tasks, high precision, and strict quality standards. Industry 4.0 can enhance these operations by:
- Improving efficiency: Automated systems can handle tasks faster and more consistently.
- Enhancing flexibility: Smart systems can adapt to varying product designs and production demands.
- Ensuring quality: Real-time monitoring and AI-powered defect detection reduce errors.
Guide to implementing Industry 4.0 in industrial assembly
Step 1: Assess current assembly processes – Begin by evaluating the strengths and weaknesses of your existing assembly line.
- Map the workflow: Document each stage of the assembly process to identify bottlenecks or inefficiencies.
- Evaluate technology readiness: Check if your current equipment and machinery support digital upgrades or if new machinery installations will be needed.
- Set objectives: Define clear goals, such as reducing cycle time, improving accuracy, or increasing output.
Practical outcome: A clear understanding of your assembly process, enabling targeted upgrades.
Step 2: Choose the right technologies – Select Industry 4.0 technologies that align with your assembly line’s requirements and objectives. The key technologies for assembly are:
- Collaborative robots (Cobots): Perform repetitive tasks like screwing, welding, or packaging with high precision, working alongside human workers.
- IoT sensors: Monitor machine performance, identify bottlenecks, and ensure real-time data sharing.
- AI and machine vision: Detect assembly defects, measure components, and ensure alignment in real-time.
- Augmented reality (AR): Provide workers with step-by-step instructions or overlay component guides for complex assemblies.
- Digital twins: Create virtual replicas of the assembly line to simulate changes and optimise processes.
Practical outcome: A tailored technology stack that addresses specific pain points in your assembly process.
Step 3: Upgrade equipment and connectivity – For a successful Industry 4.0 transition, your assembly line must support connectivity and data sharing.
- Replace or retrofit machinery: Ensure machines are IoT-enabled or can be retrofitted with sensors.
- Establish connectivity: Install a robust industrial network (e.g., 5G or Wi-Fi 6) for seamless communication between devices.
- Adopt edge computing: Use localised data processing to reduce latency for real-time decisions.
Practical outcome: An interconnected and responsive assembly line capable of leveraging Industry 4.0 technologies.
Step 4: Implement automation and data analytics – Automation and analytics are at the heart of Industry 4.0, transforming manual assembly into an intelligent, data-driven process. Key actions are:
- Deploy robotic systems: Integrate robots to automate repetitive tasks, ensuring precision and reducing worker fatigue.
- Enable predictive maintenance: Use IoT data to predict and prevent equipment failures, reducing downtime.
- Utilise big data analytics: Analyse assembly line data to identify inefficiencies and optimise workflows.
Practical outcome: A smarter assembly process with automated systems and continuous performance insights.
Step 5: Train your workforce – The transition to Industry 4.0 requires a skilled workforce capable of operating and maintaining new technologies. Key actions are:
- Provide hands-on training: Teach workers how to use collaborative robots, AR devices, and other tools.
- Foster digital literacy: Help employees interpret data insights and make informed decisions.
- Encourage cross-functional collaboration: Promote teamwork between operators, IT professionals, and engineers.
Practical outcome: A skilled and adaptable workforce that drives the success of your Industry 4.0 assembly line.
Step 6: Monitor, optimise, and scale – Once implemented, continuously monitor the assembly process to ensure optimal performance and identify areas for improvement.
- Track KPIs: Measure metrics such as production speed, defect rates, and machine uptime.
- Use digital twins: Simulate process changes to predict their impact before implementation.
- Expand to other lines: Scale successful practices and technologies to additional assembly lines or processes.
Practical outcome: A dynamic and evolving assembly system that remains competitive in the face of changing demands.
Benefits of implementing Industry 4.0 in assembly
- Increased efficiency: Streamlined processes, reduced downtime, and improved productivity.
- Enhanced quality: Improved product quality through automated inspections and real-time monitoring.
- Improved flexibility: Faster time-to-market and ability to adapt to changing customer demands.
- Reduced costs: Lower labour costs, reduced waste, and optimised resource utilisation.
- Enhanced safety: Reduced risk of accidents and injuries through automation and remote monitoring.
Challenges and how to overcome them:
One major challenge is high implementation costs, which can be addressed by starting with small-scale pilot projects in high-impact areas. This approach allows for a manageable initial investment and provides an opportunity to demonstrate ROI before scaling up.
Resistance to change is another common obstacle. Overcoming this requires involving employees early in the transition, clearly communicating the benefits, and offering training to build their confidence and skills in using new systems.
Cybersecurity risks are a significant concern, especially with increased connectivity. To mitigate these risks, it’s essential to invest in robust firewalls, encryption, and threat detection systems, ensuring the security of connected infrastructure.
Lastly, integration complexity can pose difficulties when new technologies need to work with existing systems. This challenge can be overcome by partnering with experienced providers or consultants who can facilitate seamless technology integration, ensuring minimal disruption and a smooth transition.
Beck & Pollitzer: Your partner in Industry 4.0 transformation
In an era where precision and agility are paramount, transitioning your assembly line to Industry 4.0 is not just a competitive advantage; it’s a necessity for staying ahead in the rapidly evolving industrial landscape.
Implementing Industry 4.0 in your assembly processes requires careful planning, skilled professionals, and the right technical expertise. Beck & Pollitzer is your one-stop shop for navigating this transformation journey. Our comprehensive suite of services encompasses every step of the process, from:
- Machinery installation and removal: Our experienced technicians ensure seamless installation of new, Industry 4.0-compatible machinery and removal of outdated equipment. Read more about our Machinery removal and installation services.
- Electrical integration and design: Our electrical specialists design and install robust electrical systems to support the increased data flow and connectivity demands of Industry 4.0.
- Mechanical assemblies: We can handle all complex mechanical assemblies, ensuring your new equipment integrates flawlessly into your existing assembly line.
- Project management: Beck & Pollitzer provide dedicated project managers to oversee the entire implementation process, ensuring it stays on track and within budget.
- Machinery modification and relocation: Our skilled engineers can modify existing machinery to make them Industry 4.0 ready, or relocate them to optimise your production layout.
- Maintenance and commissioning support: We offer ongoing maintenance and commissioning support to ensure your Industry 4.0 assembly line operates at peak performance.
By leveraging our over 160 years of experience and partnering with leading technology providers, Beck & Pollitzer can help you overcome the challenges of Industry 4.0 adoption and unlock the full potential of smart manufacturing. We will work closely with you to assess your current assembly processes, identify the most suitable Industry 4.0 technologies, and implement a customised solution that delivers tangible results.
Explore our case studies to discover how Beck & Pollitzer tackles Industry 4.0 challenges across various industries: https://beck-pollitzer.com/latest-news/. Let Beck & Pollitzer be your trusted partner in achieving a future-proof, intelligent assembly line. Call us today to learn more about our services and how we can help you embrace Industry 4.0.